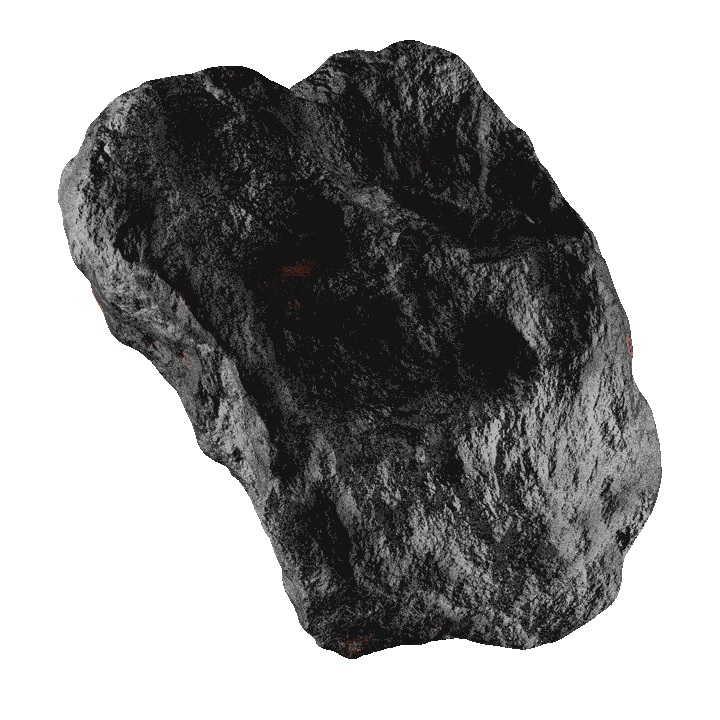
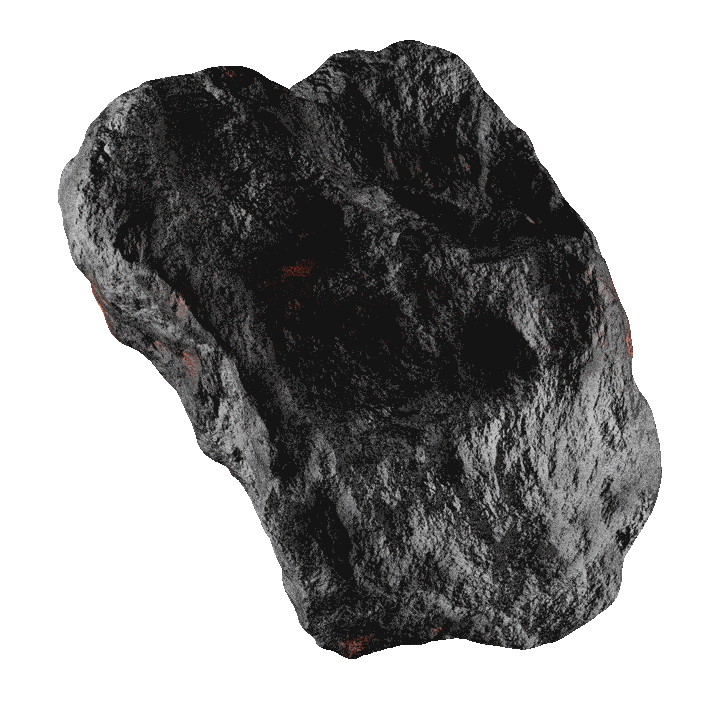
Iron Ore
Iron is one of the most widely used metals in the world, accounting for approximately 95% of the total metallic tonnage present. It can confidently be claimed that the majority of the iron ore extracted worldwide is used in the production of raw iron, which serves as the primary material for steel manufacturing. There remains a small amount of iron ore that has diverse applications.
Iron ore is one of the most important mineral resources on Earth and is recognized as the raw material for steel production. Are you familiar with its properties and composition? Do you know how this material is extracted? Are you acquainted with its applications? To learn more about this mineral, its properties, and applications, stay with us.
What is Iron Ore and Where is it Found?
Iron is a metallic element that constitutes approximately 5% of the Earth’s crust and is the fourth most abundant element in the crust. The most important deposits of this element on Earth are found in sedimentary rocks in iron ore mines. Iron ore is a rock from which iron metal can be economically extracted. This mineral is formed by chemical reactions that have resulted in the combination of iron and oxygen. Two important mineral substances in these significant deposits are hematite and magnetite.
Formation of Iron Rocks
As this mineral is one of the most important and widely used mineral rocks globally, the question arises: what is iron ore? How is it formed, and what is its raw material? In response to this question, it can be said that almost everything recognized as iron ore in the world formed and was deposited approximately 1.8 billion years ago.
At that time, the oceans of the Earth contained a significant amount of dissolved iron, but there was no dissolved oxygen in these oceans. With the onset of photosynthesis by the earliest organisms in the world, oxygen was generated in the ocean waters. Consequently, iron deposits began to form in the presence of oxygen.
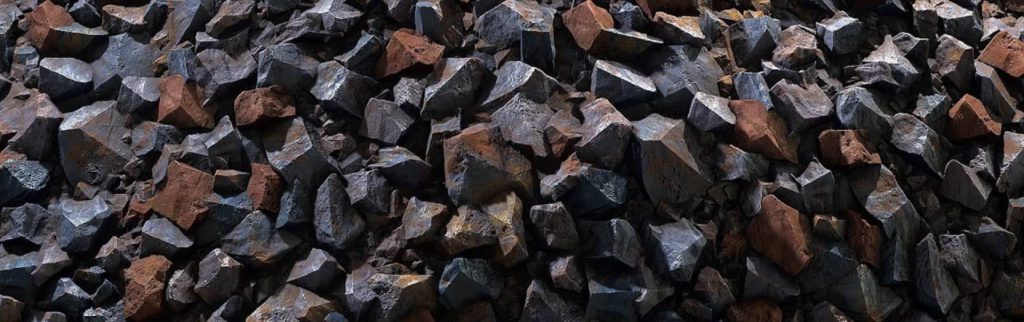
Specifications of Hematite Iron Ore and Its Uses
Hematite is one of the iron oxide minerals. This mineral has a chemical formula of Fe2O3. One of the characteristics of hematite iron ore is that it is non-magnetic, and the color variations of this mineral range from steel gray to reddish-brown. Pure hematite contains 69.9% iron. This mineral is used in coloring and the production of stainless steel. Since the early 1960s, hematite has been the dominant iron ore extracted in Australia, and nearly 96% of Australia’s iron ore exports are hematite, most of which is extracted from the deposits in Hamersley Province in Western Australia.
Specifications of Magnetite Iron Ore
One of the minerals with a higher iron content is called magnetite, which is derived from the Greek word meaning “lodestone.” The chemical formula of this iron ore mineral is Fe3O4, and its maximum purity contains 70% iron (Fe). However, there are other types of iron ores known by their constituent minerals, such as zeolite, limonite, siderite, greenschist, and marcasite.
Extraction and Processing Stages of Iron Ore
The extraction and processing of iron ore involve multiple stages, which are briefly described as follows:
Exploration and identification of deposits
The first step usually involves identifying areas where iron ore deposits are believed to exist. Various methods are used for identification, including aerial photography, geochemistry, geological mapping, borehole drilling, electrical surveys, and geophysical surveys.
Sampling of deposits
After the discovery of a deposit, sampling must be done. This process involves both partial and comprehensive sampling, and the collected samples are transferred to laboratories for detailed analysis.
Legal registration of iron ore deposits
After sampling, the next step is the legal registration of the discovered deposits. The Ministry of Industry, Mine, and Trade (MIMT) examines the designated area, and if no issues arise, the necessary administrative procedures and document submission result in the registration of the mine under the applicant’s name.
Mining operations
Mining is the next stage in the process. To determine the appropriate mining and extraction methods, various factors need to be considered and thoroughly evaluated. Once a final decision is made, the mining phase can commence.
Blasting
Blasting operations occur immediately after drilling and the creation of suitable mine tunnels. During this stage, rocks are fragmented, allowing them to be extracted for further processing.
Loading of iron ore
The final stage involves loading the fragmented rocks onto suitable trucks and transporting them to the processing plant.
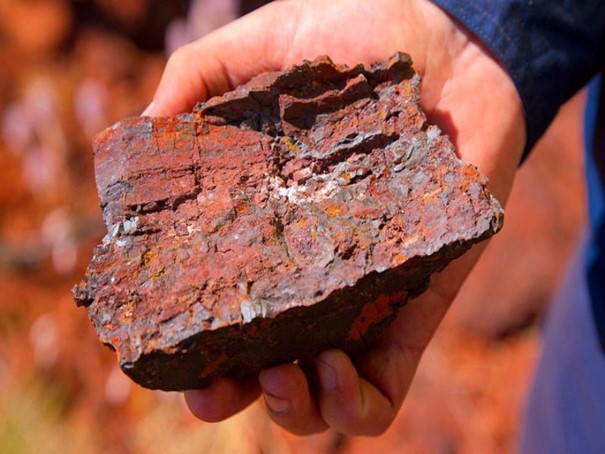
Specifications and Various Forms of Iron Ore
Iron ore exists in various forms in the market to meet the requirements of different industries for its utilization.
Graded iron ore
One type is graded iron ore, which has been used less in recent years due to its low reducibility.
Sinter
Sintering is one of the most common methods used for iron ore. Approximately 700 million tons of sinter are produced each year and used in the iron and steel industries.
Pellet or pig iron
Around 300 million tons of pellets are produced annually, with 80% of them being used in blast furnaces and the remaining 20% used for direct reduction.
Final Words
As mentioned, iron ore is the primary raw material for steel production. Approximately 98% of extracted iron ore worldwide is used for steel production. The automotive and construction industries are the main consumers of steel, and therefore, the demand and price of iron ore are influenced by these sectors. Additionally, iron ore finds miscellaneous and scattered uses. It may be used in concrete and cement production, drilling mud, coal washing, and some pigments. To receive more information and make a purchase, you can fill out the contact form on the website kaladasht.com so that the requested information will be available to you.
Frequently Asked Questions (FAQs)
Iron ore is a metallic element that constitutes approximately 5% of the Earth’s crust. When this raw material is extracted from the ground and impurities are separated, it forms a dark silver-brown powder. This element readily oxidizes, and it is generally not usable in its pure and solid form.
Iron ore powder is primarily used to enhance the strength of various components, such as in construction and alloy production, with its main use in the steel production chain.
The most common elements used in alloy production along with iron ore are nickel and chromium.
China is the largest consumer in the global steel industry. In terms of production, Australia is the main producer of this material worldwide, followed by China and Brazil.